What is the Importance of Pretreatment for Industrial Reverse Osmosis Water Treatment
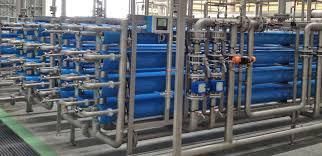
Your body is a machine. Like most machines, you have to properly maintain your body in order for it to function properly. Along with regular cleaning and checkups, you also have to be cognizant of what food you put into your body or else it won’t work at its maximum potential. An industrial reverse osmosis water treatment system actually works in quite a similar way. Regular cleaning and maintenance will certainly help keep everything running in optimal shape, but making sure that you are not putting the wrong things through the system is what really counts in the long run.
In this case, the “food” is the effluent being pumped through the system. Certain constituents can foul the system membranes, which can reduce the water flow or cause damage to these membrane filters.
It is important to ensure that any potential foulants are removed prior to contact with the membranes. To do so, proper pretreatment steps are vital to the longevity and successful operation of the industrial reverse osmosis water treatment system.
What issues can arise with RO operations?
Certain biologic or mineral contaminants cause industrial reverse osmosis membranes to “foul” or “scale”, but what exactly does that mean and how does that affect the system?
Fouling is what happens when suspended or dissolved contaminants in the wastewater stream deposit and build up on the surface of the membranes.
Scaling is similar in its effects, but it occurs when the concentration of mineral salts in the reject waste stream become high enough to over-saturate the water and begin precipitating. These precipitants are then deposited onto the membrane surfaces.
The overall effect of RO membrane fouling and/or scaling is the decline in production. This decline is caused by altered flow and pressure which can also drive up operating costs and energy consumption as a result.
As foulants and/or scalants build up on and around the membranes surface, water cannot easily pass through the membrane and water flow is reduced as a result. In addition, the increased concentration of contaminants in the reject water increases the osmotic pressure. Pressures outside the range of the design specification of the membrane can cause damage, and the membrane will need to be completely replaced earlier than necessary.
Changes in pressure in particular affect the costs of industrial reverse osmosis water treatment operation. High pressure pumps may have to work harder which will then drive up energy consumption and its associated costs.
What causes these fouling/scaling issues to occur?
This is an incomplete list of possible constituents that can cause fouling or scaling. This list is divided into general categories of wastewater or seawater compositions. Analysis should be performed on the industrial water or wastewater sources to determine the exact components that would be of concern for an industrial reverse osmosis system.
Fouling
Colloids: clays, flocs (turbidity and suspended solids)
Biological: microorganisms, bacteria, viruses, protozoa
Organics: oils, polyelectrolytes, humics, biopolymers, tannins
Scaling
Minerals: sulfates, calcium, magnesium, carbonates, silica
What pre-treatment methods can optimize an industrial reverse osmosis water treatment process:
Here are a few of the possible pre-treatment processes for an RO system. These tend to cover a wide range of contaminants, but are not all encompassing. Proper pre-treatment solutions should be tailored to the results of a wastewater/seawater analysis.
Filtration (cartridge): for colloids, some organics and biological contaminants
Anti-scalant: for mineral scaling
Coagulation: for organics, colloids, and some minerals and biological pollutants
Aside from pre-treatment, it is important to monitor other factors (those specified by the RO system manufacturer and designer) to reduce the chance of fouling and scaling and keep the system working optimally. Several of the operating conditions that affect performance are solution pH, solution temperature, and recovery rate.
Temperature and pH affect the formation of scale precipitants. Higher pH levels increases their concentration and lower temperatures reduce solubility.
Recovery rate is defined as the ratio of the permeate flow to feed flow. Though perhaps not ideal for production, reducing this recovery rate helps reduce fouling. Increasing the feed flow rate or decreasing the operating pressure will reduce the recovery rate. The goal is to reduce the concentration of all substances in the system so they will not reach the saturation limit.
If you want to keep your RO systems working efficiently for a long time, you need to make sure to take care of the membranes. Proper pre-treatment, maintenance, and operation will prevent system fouling and scaling and prolong the life of your membranes. This method ensures your industrial reverse osmosis water treatment system is providing you with the cleanest water possible at an optimized.
Are you using or thinking about implementing an industrial reverse osmosis water treatment system in your companies operations? Do you know your RO pretreatment options?
Contact the water specialists at Genesis Water Technologies, Inc. at 1-877-267-3699 or reach out to us via email at customersupport@genesiswatertech.com to connect with one of our representatives for a free initial consultation. We look forward to assisting you in your specific industrial water treatment & reuse applications.