Textile Wastewater Treatment Systems: Sustainable Solutions for Compliance & Cost Savings
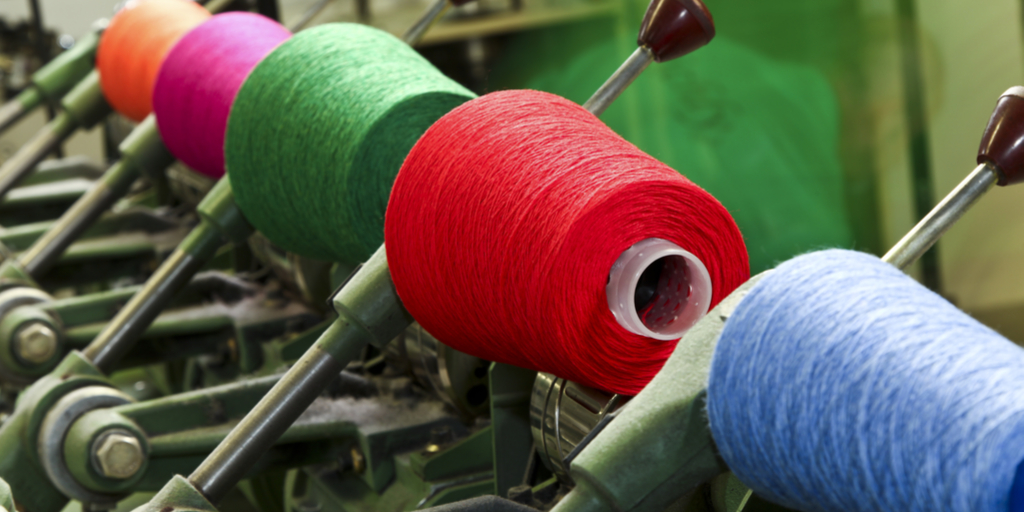
In the textile industry, water is essential, but this reliance creates a wastewater challenge. Effective textile wastewater treatment systems are crucial for both the environment and a company’s bottom line. Let’s explore why these systems matter and how the right approach can transform wastewater from a problem into a resource.
From fiber production to garment finishing, every step uses water, creating wastewater containing dyes, chemicals, starches, and oils. Without proper treatment, these pollutants harm ecosystems and human health, as many textile wastewater chemicals are mutagenic and carcinogenic.
Textile wastewater characteristics necessitate these treatment processes to remove synthetic dyes, sizing agents, suspended solids and trace heavy metals.
Table of Contents:
- The Impact of Untreated Textile Wastewater
- Textile Wastewater Treatment Systems: An In-Depth Look
- Advanced Textile Wastewater Treatment Systems: Enhanced Purification
- Regulations and Compliance for Textile Wastewater Treatment
- Transforming Challenges into Opportunities
- FAQs about Textile wastewater treatment systems
- Conclusion
The Impact of Untreated Textile Wastewater
Imagine brightly colored dyes, harsh chemicals, suspended solids and vast amounts of water used in textile production going directly back into our water systems. That’s the reality without effective textile wastewater treatment systems. The fashion industry significantly contributes to water pollution. These pollutants damage aquatic life, contaminate soil, and impact local communities.
Textile Wastewater Treatment Systems: An In-Depth Review
Different textile processes generate different kinds of wastewater. From sizing and de-sizing to scouring, bleaching, dyeing, printing, and finishing, each stage adds its own pollutants. These stages often involve byproducts of starches impacting sizing and finishing, causing additional dye penetration and contamination from various chemicals.
Dyeing and printing in particular contribute significantly to contaminated wastewater, introducing dyes pigments, and other harmful substances. A comprehensive wastewater treatment strategy considers each of these processes and the specific waste produced to determine which sustainable wastewater treatment solution will be the most effective for each facility.
Many businesses find biological treatment combined with microbubble jet aeration to be among the most efficient ways to achieve excellent results, especially when trying to remove dye molecules, organic compounds, and other harmful byproducts introduced through sizing, de-sizing, scouring, bleaching, and mercerizing.
Common Treatment Methods:
- Coagulation and Flocculation: This adds chemicals to clump pollutants together for easier removal. Coagulation and flocculation are often a first step in effectively treating water within the textile industry. Solutions like Zeoturb liquid bio-organic flocculant can be beneficial in this process.
- Biological Treatment: This uses microorganisms to break down organic pollutants. Activated sludge systems are a common example, often using aeration. You can learn about products like the Mbio MBBR media, jet aeration systems and Biostik modules for biological methods.
- Membrane Filtration: This separates pollutants by size and charge using membranes like reverse osmosis, nanofiltration, and ultrafiltration systems. Products like Tertiary Wastewater Reverse Osmosis, GCAT catalytic activation treatment systems and Natzeo Treatment Media can be part of the pretreatment for these systems.
- Adsorption: This uses materials like coconut shell activated carbon media to trap pollutants. This adsorption treatment method is part of tertiary treatment that ensures compliance with strict discharge limits within a wastewater treatment plant.
Advanced Textile Wastewater Treatment Systems: Enhanced Purification
Standard methods are a good start, but advanced technologies like advanced oxidation processes (AOPs) or membrane bioreactors (MBRs), which may utilize Zeoturb liquid bioflocculant, enhance efficiency and produce cleaner results.
Advanced oxidation processes like Genclean-Ind generate reactive oxygen compounds and hydroxyl radicals to treat water.
These systems enable treated water to meet strict reuse requirements, reducing a company’s water footprint.
Specialized membranes can be another popular choice in the textile industry because of their ability to withstand a wide range of temperatures and pressures, and their effectiveness at filtering harmful substances out of water that is used for textile manufacturing.
Regulations and Compliance for Textile Wastewater Treatment
Textile plants face strict regulations on wastewater discharge to protect the environment. Guidelines from the Environmental Protection Agency and international organizations like the Zero Discharge of Hazardous Chemicals (ZDHC) Foundation provide a framework.
Textile wastewater treatment systems must be tailored, as many textile wastewater treatments generate harmful byproducts, including high-strength toxins from various chemicals, dyes, and starches.
Sustainable solutions within wastewater management ensure plants stay compliant with environmental standards and minimize environmental impact from trace heavy metals and synthetic dyes present in wastewater discharge.
Businesses within the textile industry, particularly those dealing with fustian fur and other specialized materials, should also have a treatment plan that incorporates regular testing and adjustment based on the specific needs of each plant.
Additionally, the type of material being produced would be evaluated, in order to minimize environmental impacts and remain in compliance with any environmental regulations.
Transforming Challenges into Opportunities
Textile wastewater treatment systems have gained importance due to water scarcity, pushing plants toward resource efficiency. Wastewater reuse lowers operating costs and creates new opportunities, reducing reliance on fresh water.
Reclaimed water can be used in cooling towers or boiler feedwater. Specialized wastewater treatment methods reduce high disposal costs. This demonstrates a commitment to water sustainability.
It also impacts how sizing de-sizing, scouring, bleaching, and mercerizing impact other operations such as dyeing printing of materials throughout the production process of many materials, and allows textile businesses to save money.
Proper treatment can prevent environmental issues and provide a wastewater discharge that is within compliance of all applicable standards.
Developing a treatment plan ensures consistent results and a clear process that is easy for all team members to understand. MBBR systems, as part of the treatment process have excellent case studies in these applications.
Here’s a comparison of wastewater treatments and their benefits:
Treatment Method | Benefit | Notes |
---|---|---|
Coagulation/Flocculation | Cost-effective removal of suspended solids, color, trace metals, and organics | Suitable for primary and secondary treatment processes |
Biological Treatment | Effective for organic pollutants. | Requires primary treatment. |
Membrane Filtration (RO, UF, NF) | High-quality effluent suitable for reuse. | Higher initial cost. |
Adsorption | Removes color and other specific pollutants. | Media requires replacement. |
Advanced Oxidation (AOP) | Breaks down tough-to-treat pollutants. | Most advanced, suitable for complex wastewater. |
FAQs about Textile wastewater treatment systems
What is textile wastewater treatment?
Textile wastewater treatment removes pollutants from textile manufacturing wastewater. These methods purify water for discharge, reuse, or recycling.
What are the 4 types of wastewater treatment?
The four types are preliminary, primary, secondary, and tertiary, using physical, chemical, and biological processes across different stages. These different types of treatment methods may utilize MBBR, AOP, catalytic treatment or electrocoagulation solutions in order to purify wastewater to the appropriate levels.
What are the wastewater characteristics of the textile industry?
Textile industry wastewater is chemically complex, loaded with dyes, sizing agents, suspended solids, and more. Its varying pH and temperature often require tailored treatment systems and regular maintenance to ensure optimal performance.
Conclusion
As the textile industry faces mounting environmental and regulatory challenges, adopting innovative wastewater treatment solutions is no longer optional—it’s essential. Sustainable technologies like Zeoturb bio-organic flocculant, electrocoagulation, GCAT catalytic activation technology, and microbubble aeration not only improve effluent quality but also reduce operating costs, sludge generation, and chemical dependency.
By integrating these advanced treatment methods, textile manufacturers can achieve regulatory compliance, enhance sustainability, and improve water reuse efficiency—leading to a competitive advantage in an increasingly eco-conscious market.
Ready to optimize your textile wastewater treatment process? Contact the water treatment specialists at Genesis Water Technologies today for a consultation and discover how our cutting-edge solutions can help you reduce costs, improve compliance, and enhance sustainability.
Schedule a Consultation Now – Let’s create a cleaner, more sustainable future for the textile industry—together! Click here to get started!