Effective Silica Removal for Industrial Water Treatment
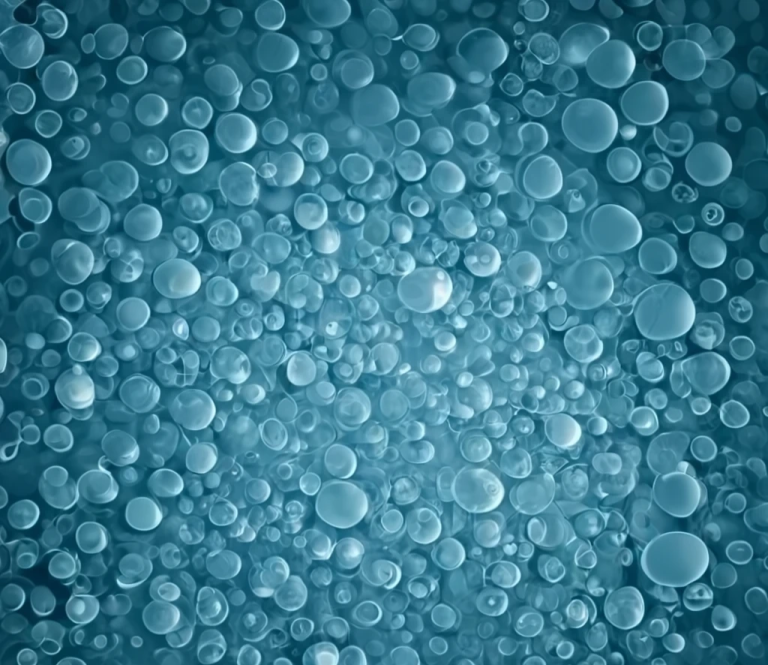
In the never-ending quest for optimal water treatment, industrial plant managers and engineers know that silica removal is the backbone of effective system management. Reduce silica, and your equipment will thank you – minimizing costly repairs and downtime.
Imagine you’re at the helm of a boat, navigating through a sea of choices for silica removal methods. With multiple options available, including lime softening, catalytic media, electrocoagulation and reverse osmosis, selecting the right one for your specific needs can be overwhelming. But fear not! We’re about to set a course for a deeper dive into each of these methods, helping you make an informed decision.
Silica removal systems are built on a foundation of four key elements: raw water quality, target silica levels, type of silica, and the ability to maintain the system over time. Each of these factors must be carefully considered to ensure the system is operating efficiently and effectively.
Table of Contents:
- What Is Silica and Why Is Removal Necessary?
- Common Methods for Removing Silica from Water
- Designing an Effective Water Treatment System for Silica Removal
- Choosing the Best Silica Removal Method for Your Needs
- FAQs in Relation to Silica Removal
- Conclusion
What Is Silica and Why Is Removal Necessary?
Silica is a surprising veteran of the Earth’s terrain, popping up in all sorts of geological settings. Yet, in the pursuit of innovation, we cannot neglect the tiny and tangible, mineral contaminants like silica that crop up in our industrial source water analysis.
What is silica?
A mere stone’s throw away from our homes and places of business lies the often-overlooked world of silicon dioxide. Silica, also known as silicon dioxide (SiO₂), is a natural compound made of silicon and oxygen. It is a key component of the earth’s crust and is commonly found in materials such as sand, quartz, and various types of rock.
Silica can exist in water in several forms, relatively large particles known as silica granules called particulate silica, finer suspended particles called colloidal silica, reactive ionic silica and dissolved silica. The form of silica present depends on factors like pH, temperature, and the water source.
Why is silica removal necessary?
Even moderate silica levels in water can lead to problems in industrial operations. Under these conditions, silica deposits harden into virtually non removable barriers that compromise heat exchange, modify pressure boundaries, and deteriorate membrane filters.
Effective silica removal is a lifeline for machinery that relies on large amounts of water, such as cooling towers and boilers. Failure to remove silica can lead to reduced performance, constant maintenance headaches, and premature equipment breakdown.
Issues Associated with High Silica levels in water:
The higher the silica levels in water, the greater the risk of silica-related issues. Some common problems caused by elevated silica content include:
- Scale deposits on heat transfer surfaces that act as insulators and reduce efficiency.
- Silica particles interfering with desired pressure ranges in equipment.
- Membrane fouling in RO systems and other filtration units.
- Abrasion and wear of moving parts and surfaces.
- Frequent equipment downtime for cleaning and repairs.
A critical issue faced by industries including the power generation, microelectronics manufacturing, and mining sectors is the buildup of excess silica in their raw water sources.
Based on the region of the world your company is located determines the quality of the raw water sources that you have available to your operations. In regions with high silica source water, to ensure long-term sustainability, eliminating silicon dioxide from water supplies becomes crucial to optimize operating cost of plant operations.
Common Methods for Removing Silica from Water
So how do you actually remove silica from water? There are several methods commonly used in industrial water treatment, each with its own strengths and limitations. Let’s take a closer look.
Lime softening for silica removal
One of the most common approaches for removing silica, especially larger silica particles, is lime softening. This involves adding calcium hydroxide (lime) to the water to raise the pH and trigger the precipitation of silica along with hardness minerals like calcium and magnesium.
The precipitated solids form flocs that settle out of solution, taking the silica with them. Lime softening is often used as a pretreatment step before other silica removal technologies to reduce the overall silica load.
Catalytic Ceramic Media
Catalytic ceramic media are specialized filtration materials used in water treatment processes to remove contaminants, including silica. This media leverages the catalytic properties of specialized ceramics to enhance the efficiency and effectiveness of filtration systems.
Catalytic ceramic media offer a robust and efficient solution for silica reduction, leveraging advanced materials science to enhance water quality and system performance. This is especially relevant in lower TDS water sources.
However, proper system design and maintenance are essential to maximize the benefits of catalytic ceramic media as a suitable pretreatment prior to polishing membrane systems such as reverse osmosis. The G-CAT catalytic media system is one such system deploying this unique technology.
Reverse osmosis for silica removal
Reverse osmosis (RO) membranes can remove over 95% of dissolved silica by using pressure to force water through a semi-permeable membrane. The silica is left behind in the concentrate stream.
RO is very effective but is also prone to silica scaling on the membrane surface, which limits water recovery. Pretreatment using catalytic ceramic media, ultrafiltration or electrocoagulation before an RO system can increase permeate flow rates and notably reduce operation costs.
Ultrafiltration for removing colloidal silica
For very fine colloidal silica particles, ultrafiltration (UF) membranes with pore sizes small enough to capture the silica can be used. The silica is physically “sieved” out of the water.
UF is often preceded by a coagulation step such as electrocoagulation or Zeoturb natural polymer flocculation to aggregate the colloidal particles and improve removal efficiency. UF does not remove dissolved silica, so it may be combined with other methods such as RO for complete silica removal.
Electrocoagulation for silica removal
Innovative electrocoagulation technology deploys electricity to release metal ions from electrodes, usually designed from aluminum or iron. These ions flocculate together, gathering the silicon and other pollutants and causing them to coalesce, yielding cleaner results.
Electrocoagulation can handle high silica loads and produces less waste than chemical treatment. However, this technology typically requires a certain minimal level of conductivity to operate efficiently. In these cases, it is very effective at removing colloidal silica but may need to be combined with other methods such as RO for dissolved silica.
Designing an Effective Water Treatment System for Silica Removal
No two silica removal systems are the same, and that’s why it’s essential to develop a treatment plan that’s uniquely suited to your specific application requirements. From selecting the right treatment technology to choosing the most effective treatment chemicals, every decision counts.
Considerations for raw water quality
Before designing a silica removal system, it’s essential to get a detailed understanding of the source water being used in your operations. That means analyzing the water quality and composition, including the concentration of silica and its distribution in colloidal, dissolved, and reactive forms.
Clear guidance: pH, mineral hardness, and the presence of organic matter and competing ions all conspire to create the perfect symphony of water treatment. The melody changes with the seasons, forcing us to harmonize with seasonal water quality fluctuations.
Combining silica removal technologies
Achieving the required silica levels often means using multiple removal technologies in series based on the source water quality. For example, electrocoagulation combined with natural polymer flocculation in combination with RO with specific antiscalant for high-silica waters.
Scaling is a persistent problem for reverse osmosis systems. To mitigate this issue especially in lower TDS source water is by using specialized catalytic ceramic media along with specific antiscalants. This approach can optimize the treatment process. The ideal treatment approach hinges on a thorough understanding of the raw water composition and conducting process optimization treatability testing to determine the most appropriate treatment strategy.
Achieving required silica levels for application
The target silica level for the treated water depends on its end use. Makeup water for high-pressure boilers and feed water for semiconductor manufacturing often have very stringent requirements, sometimes under 0.02 mg/L as SiO2.
Careful treatability testing is recommended to validate that the proposed treatment system can reliably produce water that meets the required water quality guidelines for the application. Online silica analyzers are very useful for monitoring treatment plant performance.
Choosing the Best Silica Removal Method for Your Needs
With several silica removal methods available, each with different capabilities and trade-offs, how do you select the right approach for your application? Here are the key considerations.
Factors affecting silica removal method selection
Making the right choice of silica removal technology hinges on several critical factors. These include the type and quantity of impurities present, the preferred purification level, and the physical and chemical properties of the substance.
- Silica concentration and forms (colloidal, dissolved, reactive)
- Required finished water quality
- Raw water chemistry (TDS, pH, hardness, competing ions)
- Available footprint and capital budget
- Desired level of automation and operator attention
- Waste disposal options and costs
When evaluating the variables involved, it becomes clearer which treatment approaches are most feasible and applicable for a given application.
Comparing silica removal methods for raw water treatment
Each silica removal method has its strengths and limitations that must be weighed against the project constraints and priorities. For example:
- Lime softening has low operating costs but requires significant space and generates a lot of sludge.
- RO provides excellent silica removal but has high capital and energy costs and is prone to scaling.
- Electrocoagulation has a small footprint but higher capital costs and requires a minimal level of conductivity to be efficient.
- Ultrafiltration has good silica removal capabilities for colloidal silica but not for other forms of silica and it can also be prone to scaling.
- Catalytic media has a small footprint and low operating costs but does requires post filtration systems to optimize silica removal.
Treatability testing using different treatment methods with the actual source water is very valuable for comparing performance and identifying potential issues prior to full-scale implementation.
Case studies of successful silica removal systems
Touting supreme environmental responsiveness, the below case examples show successful implementation of silica removal systems.
- A power plant that used catalytic media along with RO and specific antiscalant injection to reduce boiler feed water silica from 30 mg/L to under 0.2 mg/L, preventing turbine scaling.
- A microelectronics manufacturer that used catalytic media along with RO to produce ultrapure water with silica under 1 ug/L for wafer rinsing.
- A mining operation that used electrocoagulation to remove over 90% of colloidal silica from tailings pond water for reuse in the process.
- A bottled water operation using a high silica municipal feed source that used catalytic media along with RO and antiscalant injection to reduce silica levels below < 0.2 mg/l.
- A beverage company using a high silica low TDS feed source using catalytic media along with RO and antiscalant injection to reduce TDS and prevent membrane fouling.
Examining relevant case studies can provide valuable insights into the real-world performance and operational considerations of different silica removal approaches.
In Summary:
Effective silica removal in industrial water treatment involves a combination of methods tailored to the specific application, including lime softening, catalytic media, reverse osmosis, ultrafiltration, and electrocoagulation, to remove both colloidal and dissolved silica forms and prevent scaling, equipment damage, and process downtime.
FAQs in Relation to Silica Removal
What removes silica?
The most effective methods for removing silica include lime softening, ion exchange, reverse osmosis, and ultrafiltration. Think of these technologies as a team of specialized detectives, each with its own unique approach to tracking down and capturing silica particles, leaving your water supply silica-free.
What chemical removes silica scales?
Calcium hydroxide, also known as lime, is commonly used to remove silica scales. It works like a cleaning agent, neutralizing the scales and allowing them to be removed. However, this requires a large footprint and produced a lot of sludge.
Zeoturb, a bio-organic liquid flocculant is used alongside specialized electrocoagulation to optimize silica scale removal.
Conclusion
Navigating the complexities of silica removal in water treatment is essential for ensuring the longevity and efficiency of your industrial systems. By understanding the various methods available—such as lime softening, reverse osmosis, ultrafiltration, and catalytic ceramic media—you can tailor a solution that meets your specific needs and operational goals. Each method has unique strengths and applications, making it crucial to evaluate your raw water quality, target silica levels, and system maintenance requirements.
Reducing silica not only protects your equipment from scaling and fouling but also minimizes costly repairs and downtime, ensuring your operations run smoothly. Whether you’re dealing with high silica content in feed water for power plants, microelectronics manufacturing, or beverage production, adopting the right combination of technologies can make all the difference.
Ready to optimize your water treatment system and protect your investments?
Contact the team of water specialists at Genesis Water Technologies today at +1 877 267 3699 or via email at customersupport@genesiswatertech.com for a consultation to determine an optimal silica removal solution tailored to your needs. Let’s work together to enhance your water quality and operational efficiency, ensuring long-term success and sustainability.
Take the first step towards cleaner water and more efficient operations—reach out to us now!