How to Minimize Silica Scale in Process Water: A Practical Guide
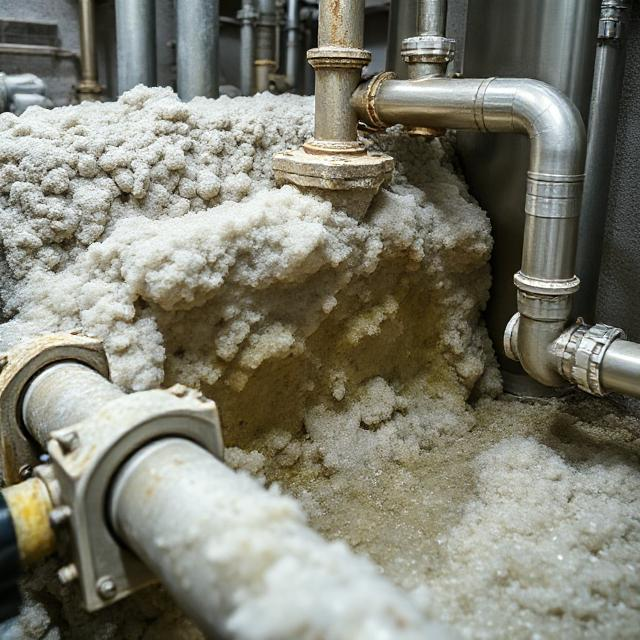
Have you noticed a decline in the performance of your water-cooled equipment? For many manufacturing plant operators and engineers, one of the primary challenges is how to minimize silica scale in process water. Many sustainability professionals find that to minimize silica build-up in process equipment is a struggle, often leading to significant operational challenges.
Silica, a prevalent substance in groundwater, seems to have a Jekyll and Hyde nature, going from a dissolved mineral to something causing challenges for boilers, cooling towers, RO membrane surfaces and other process equipment.
However, this issue isn’t exclusive to large industrial plants; it affects a broad spectrum of industrial applications dealing with this challenging contaminant.
Taking proactive measures now can save considerable time and resources in the long run, effectively reducing silica-related problems.
In this article, you will find a practical playbook for plant operators, consulting engineers, and the service companies that support them to handle silica remediation efficiently and sustainably.
Table of Contents
- Why Silica Scale Deserves Your Attention
- Know Your Enemy: The Three Faces of Silica
- Hidden Costs: Beyond Lost Efficiency
- A Holistic Silica Control Program
- The Importance of Partnering with Water Treatment Specialists
- Conclusion & Call to Action
- Quick‑Hit FAQ to Minimize Silica Scale in Process Water for Operators & Engineers
1. Why Silica Scale Deserves Your Attention
Silica (SiO₂) is the second‑most abundant element within the earth’s crust—and the bane of water‑cooled equipment. Once dissolved silica converts to scale, it acts like ceramic insulation on heat‑transfer surfaces, slashing efficiency, driving up fuel and electricity costs, and triggering costly unplanned shutdowns.
A single millimeter of silica scale can:
• Cut heat‑transfer efficiency by 8–10 %
• Increase boiler or chiller fuel use by 3–4 %
• Reduce membrane throughput by 5–15 %
For facilities that run 24/7, those percentages quickly snowball into seven figure or larger annual losses.
2. Know Your Enemy: The Three Faces of Silica
Understanding which form dominates in your boiler feed, make‑up or recirculating water determines the treatment process train—and whether you solve the problem or merely relocate it.
Silica Type | Typical Size | Key Challenge | Primary Countermeasure |
Granular | >1 µm | Settles but plugs strainers, drains & nozzles | Natzeo treatment media or self‑cleaning filtration |
Colloidal | 0.01–1 µm | Stays suspended; clouds water | Bio‑organic liquid flocculants (e.g., Zeoturb) + UF or low micron filtration |
Reactive (ionic) | <0.01 µm | Dissolves; forms hard, glassy scale | Ion exchange, GCAT™, RO/NF polishing |
3. Hidden Costs: Beyond Lost Efficiency
• Premature equipment failure – cracked tubes, warped plates, punctured damaged membranes
• Emergency maintenance – overtime labor, rush parts, rental boilers/chillers
• Regulatory risk – exceedance on discharge permits or OSHA silica‑dust limits during mechanical clean‑outs
• Sustainability penalties – higher Scope 1 & Scope 2 emissions from avoidable energy use due to treatment process inefficiencies
A power generation company recently documented $83 000/day in lost production when silica scale forced an unscheduled boiler outage. The fix—pretreatment upgrades plus catalytic activation treatment technology—were simulated to show the ROI for these retrofits paying for themselves in under six weeks.
4. A Holistic Silica‑Control Program
4.1 Source‑Water Audit
1. Sample & speciate silica by type (granular / colloidal / reactive).
2. Profile co‑contaminants (hardness, iron, certain organics).
3. Map seasonal swings and process water side‑streams.
4.2 Fit‑for‑Purpose Pretreatment
Objective | Tools in the Toolbox |
Bulk solids removal | Automatic self cleaning screen filters, hydrocyclones |
Colloidal silica knock‑down | Zeoturb liquid bio‑flocculant → lamella clarifier → UF, Natzeo filtration or micron filtration |
Hardness & reactive silica | Conventional Hot‑ or cold‑lime softening; weak‑base anion IX |
Brine recovery / zero‑liquid discharge | Evaporators, crystallizers |
4.3 Innovative Advanced Polishing for Hardness & Reactive Silica
• GCAT™ catalytic activation – neutralizes ionic charge and alters silica crystal structure so RO/NF can reject it.
• High‑recovery RO/NF – achieves <10 ppm silica inlet water sufficient for turbines.
• Specialized Electrocoagulation (EC) – doubles as a colloidal, heavy‑metal and oil removal step when source water conductivity is favorable for its optimal operation.
4.4 Continuous Monitoring & Optimization
• Online meters for silica, conductivity, pH, pressure differential
• Digital twins to correlate scale potential with energy KPI’s
• Quarterly membrane autopsies or tube‑sample boroscopies
• KPI review meetings—operators + engineers + service partners
5. Why Partner with a Water Treatment Specialist?
- Every plant has unique water chemistry, heat‑flux profiles, and sustainability targets. A niche water‑treatment partner such as Genesis Water Technologies brings:
- Process optimization services including Bench‑scale and pilot data to de‑risk CAPEX decisions
- Blended sustainable chemical and mechanical solutions instead of single‑vendor bias
- Regulatory foresight on tightening silica‑discharge and dust‑exposure rules
- Remote monitoring & AI‑driven set‑point control for efficient compliance
6. Conclusion & Call to Action
Minimizing silica scale in process water equipment is not a one‑size‑fits‑all exercise. It starts with a detailed silica speciation analysis, continues through tailored pretreatment and catalytic or membrane polishing, and lives or dies by real‑time monitoring and expert optimization.
Ready to cut energy costs, extend equipment life, and hit your sustainability KPIs? Talk to our water treatment specialists today by phone at 877 267 3699 or by email customersupport@genesiswatertech.com. We’ll benchmark your current losses, utilize process optimization to determine the right solution, and guarantee measurable ROI—so your boilers, cooling towers, and membrane systems run cleaner, longer, and cheaper.
Schedule an initial process‑water audit now and turn silica from your biggest headache into your easiest win!
7. Quick‑Hit FAQ for Operators & Engineers
What is the fastest way to confirm silica is my scaling culprit?
Pull a water sample and run XRF/SEM analysis or have your water testing lab run this analysis. If SiO₂ > 60 % by weight, you have a silica‑dominant scale. Pair this with a reactive‑silica test (<0.01 µm) on your process water to determine if its reactive (ionic) or not.
Can I run higher cycles of concentration in my cooling tower without scaling?
Yes—if you first knock down reactive (ionic) silica to <20 ppm and maintain LSI between –0.5 and +0.3 using threshold inhibitors or GCAT™.
Does RO always solve silica problems?
RO rejects 90–98 % reactive silica, but colloidal silica will blind the membranes unless pre‑treated using a suitable technological approach such as flocculation/GCAT/UF/EC/micron filtration. Design the whole train, not just the RO skid.
How often should I clean heat exchangers for silica?
With proper pretreatment and real‑time temperature monitoring, many plants extend cleaning intervals from monthly to annually. Trigger cleans when heat‑transfer resistance rises 15 %.