High-Efficiency Silica Treatment Methods:
Best Solutions for Industrial Water
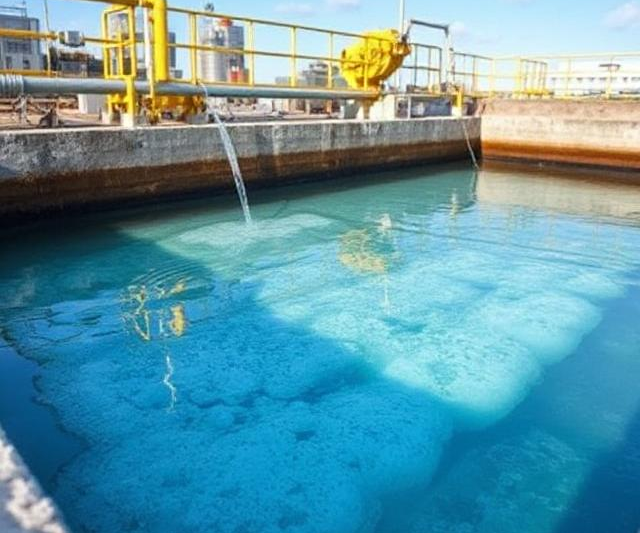
In industrial settings, high silica levels in water can damage equipment. This makes high-efficiency silica treatment methods necessary. Whether you’re a plant manager, environmental consultant, or water treatment engineer, understanding these methods is crucial for protecting your water systems and preventing costly damage.
This exploration of high-efficiency silica treatment methods will compare each option. In this article, you will learn how to make an informed water treatment decision on how to treat this particular contaminant.
Table of Contents:
- The Perils of Silica in Industrial Water
- Silica’s Multiple Forms in Water
- High-Efficiency Silica Filtration Methods
- Choosing the Right Approach: Silica Removal
- Comparing High-Efficiency Silica Filtration Methods
- Real-World Applications
- FAQs about High-efficiency silica filtration methods
- Conclusion
The Perils of Silica in Industrial Water
Silica, a common mineral found in sand, quartz, and rock, can enter water systems. While naturally occurring, silica becomes problematic when dissolved in water used in cooling towers, boilers, and industrial processes.
Excess silica forms scale deposits. These deposits disrupt operations, especially in manufacturing, by reducing flow rates and damaging equipment. The presence of silica in industrial water systems can negatively impact a large number of production processes.
The Dire Consequences of High Silica Levels
Ignoring high silica levels causes problems. Silica scale buildup on heat transfer surfaces hinders cooling tower efficiency.
Similarly, scaling in boilers reduces heat transfer and increases energy costs, reducing the equipments lifespan. Silica’s abrasive nature wears down pumps and pipelines. High silica content can have negative impacts on the water flow.
In membrane filtration systems, such as reverse osmosis (RO) and nanofiltration systems (NF), silica fouls membranes. This contaminant blocks pores, lowers system recovery efficiency, and reduces water production. Additionally, this also shortens membrane lifespans significantly and increases costs.
Addressing these risks starts with understanding silica’s behavior and its forms.
Silica’s Multiple Forms in Water
Silica exists in various forms, including reactive silica, dissolved silica, particulate silica, and colloidal silica. Knowing the type in your system determines your selection of which high-efficiency silica treatment method to choose.
Silica forms range from dissolved silica (individual molecules) to reactive silica (scale-forming). Other forms include suspended colloidal particles and larger silica granules (particulate silica). Accurately measuring different silica types, especially reactive silica, requires specialized methods.
These methods include colorimetric and atomic absorption analysis. In applications needing minimal silica content, like ultrapure water for semiconductor washing, total silica measurement is essential. Different water types may contain varying amounts of each form of silica, therefore removal efficiency varies.
High-Efficiency Silica Treatment Methods
Various methods can treat silica in the water. Choosing the right method depends on several factors, such as silica levels and budget. It is important to understand silica removal.
Other factors include operational size and financial limits. These allow plant managers to match the filtration method to their needs. This prevents excessive costs associated with silica scaling and membrane deterioration.
Lime Softening
Lime softening adjusts water pH to precipitate silica, reducing colloidal silica in industrial processes.
However, this conventional process generates large quantities of sludge which can substantially increase operational and disposal costs.
This process can contribute to overall high filtration efficiency of colloidal silica.
Ion Exchange
In the ion exchange process, specialized resins bind and remove ionic silica. Caustic soda regeneration makes them suitable for treating boiler feed water.
Its efficiency depends on competing ions. Ion exchange requires more monitoring and the use of caustic regeneration.
Therefore, it is better as a supplementary method, especially for high purity water quality applications
Reverse Osmosis (RO)
Reverse osmosis (RO) uses semi-permeable membranes to filter silica compounds. It effectively rejects dissolved silica and reactive silica.
It works best in association with specific antiscalants in high-silica water alongside catalytic treatment systems such as the GCAT for optimal performance and operational costs.
This approach optimizes reactive silica removal. It minimizes maintenance and maximizes operational effectiveness. It is essential for ensuring feed water quality meets industrial standards.
Electrocoagulation (EC)
Electrocoagulation (EC) is a batch or a continuous batch process that removes silica using charged ions. This reduces dissolved silica, preventing future downstream treatment issues while enhancing water quality.
Many consider this an effective treatment method.
This specialized technology generates less waste. Its drawback’s however, include higher capital costs and minimum water conductivity requirements for optimal operation.
EC excels at handling larger water volumes and removing smaller suspended solids like colloidal silica.
Ultrafiltration (UF)
High-efficiency silica filtration methods include ultrafiltration (UF). Its smaller pore size traps fine particulate silica through the “sieving mechanism,” but not dissolved silica or reactive silica.
Zeoturb, a bio-organic liquid flocculant, enhances UF effectiveness. Combining it with electrocoagulation also achieves high efficiency in a batch or continuous process cycle. This ensures control methods are appropriately used to address all silica types.
UF systems are easy to use and can be important for RO pretreatment if required based on a review of the source water analysis.
Genesis Catalytic Activation Treatment (G-CAT)
Specialized catalytic media can alter silica’s molecular state and neutralize its charge to improve removal by other methods.
This reduces colloidal and reactive silica preventing scaling. This method minimizes scaling and fouling in RO membranes. It’s ideal for pre membrane treatment protection.
The GWT G-CAT systems exemplify this, demonstrating how advanced catalytic activation treatment technology combined with filtration enables efficient treatment at an optimized operational cost.
Choosing the Right Approach: Silica Removal
Choosing the right high efficiency silica treatment method requires analyzing source water quality in various industrial applications.
Characteristics like pH, hardness, minerals, and organic matter must be considered. This ensures the solution aligns with objectives.
Optimized pretreatment is required to treat various types of water. This process prevents RO fouling, boosts system recovery and treatment performance.
These options include lime softening, EC with Zeoturb. as well as GCAT with specific antiscalant prior to membrane systems.
If additional polishing filtration is required. continuous electrodeionization (CEDI) further reduces silica levels without hazardous resin regeneration chemical costs.
Process optimization consulting services including treatability analysis can definitely aid in selecting the appropriate treatment approach before large-scale implementation. These services offer insights into silica behavior in different systems.
Comparing High-Efficiency Silica Treatment Methods
The best method depends on factors like space, water usage, and desired output quality.
Conventional lime softening is fine for reducing colloidal silica but not reactive or particulate forms.
Specialized EC excels using a batch or continuous batch process and higher-conductivity brackish water sources with colloidal or particulate silica, but not as much with reactive silica.
RO handles dissolved silica (reactive/colloidal) but does not handle particulate silica very well.
Choosing involves balancing strengths against limitations. Sometimes combining methods is necessary based on required treatment goals.
Method | Silica Type | Pros | Cons |
---|---|---|---|
Lime Softening | Dissolved | Low Cost | Large footprint, large sludge generation |
Ion Exchange | Reactive | High efficiency for specific silica types | Hazardous resin regeneration, monitoring |
Reverse Osmosis (RO) | Colloidal, Reactive | High rejection rate | Scaling potential, pretreatment often required |
Electrocoagulation (EC) | Colloidal, Particulate | Less waste, high silica load | Higher capital cost, source water conductivity required |
Ultrafiltration (UF) | Colloidal, Particulate | Removes fine particles | Doesn’t remove reactive silica, scaling potential requiring pretreatment |
Catalytic Activation Treatment Media | Reactive, Colloidal, Particulate | Enhances other methods, reduces scaling | Requires post-filtration |
Real-World Applications
Success stories show the impact of high-efficiency silica treatment methods. A power plant needing clean water chose GCAT catalytic treatment systems with low dose antiscalant prior to RO. The initial expense led to long-term scale reduction and higher treated water recovery rates. Their turbines stayed clean, and operating expenses notably decreased due to less maintenance.
An electronics manufacturer using GCAT catalytic treatment systems with low dose specific antiscalant and RO achieved pure water for chip rinsing.
GWT specialized EC technology helped a mining firm reuse wastewater by removing over 80% of colloidal and particulate silica. These real-world examples highlight the versatility of various treatment technologies across different industrial applications.
Conclusion
High-efficiency silica treatment is essential for industrial water systems to prevent scaling, extend equipment lifespan, and reduce operational costs in various applications from power generation to mining, manufacturing and agriculture.
From lime softening and ion exchange to reverse osmosis (RO), electrocoagulation (EC), ultrafiltration (UF), and catalytic activation treatment media, each method offers unique benefits depending on your water quality and treatment goals.
Selecting the right high-efficiency silica treatment method requires careful analysis of silica type, concentration, and system constraints. A well-optimized solution enhances system performance, reduces maintenance, and ensures long-term cost savings.
Do you need expert help in tackling your facility’s high silica water challenges?
Don’t let high silica levels damage your equipment or disrupt operations.
Contact the water treatment specialists at Genesis Water Technologies today by email at customer support@genesiswatertech.com or call +1 877 267 3699 for a free consultation and expert guidance on a suitable silica removal solution for your facility.
Let’s optimize your water treatment strategy for peak efficiency!
FAQs about High-efficiency silica filtration methods
What is the most effective filtration method?
The most effective treatment method depends on raw water silica concentration, silica types (reactive, colloidal, particulate), other impurities, and desired treated water purity. It may be used alone or with other techniques like lime softening or electrocoagulation (EC) with Zeoturb flocculant for pretreatment, reverse osmosis (RO) and continuous electrodeionization (CEDI) for polishing.
Factors such as feed water quality, pH, operational demands, silica deposits and treatment plant constraints contribute to the final determination.
Treatability studies help determine the ideal choice. Effectiveness depends on project-specific variables (factors).
What is the best way to remove silica from water?
Choosing the best removal method depends on the silica form in the raw water. Colloidal, particulate, and reactive silica behave differently.
Evaluate concentration and type and consider water quality variables. Options range from lime softening to G-CAT, RO and electrocoagulation, each with different costs and constraints.
The ideal solution must suit your facilities requirements. Several options offer a means of efficiently removing silica from the water supply.
How do you filter silica?
Silica filtration uses various methods. Whether using catalytic media like G-CAT with ultrafiltration, electrocoagulation, reverse osmosis, or ion exchange, the precise method depends on the silica type and quantity you want to remove, plus other parameters from a source water analysis.
Proper silica type analysis determines effective control measures for the silica levels in any industrial application.
Measure particulate or dissolved silica based on required purity. Consider factors like removal level and cost, tailored to your particular situation.