7 Disadvantages of the Activated Sludge Process for Municipalities and Organization
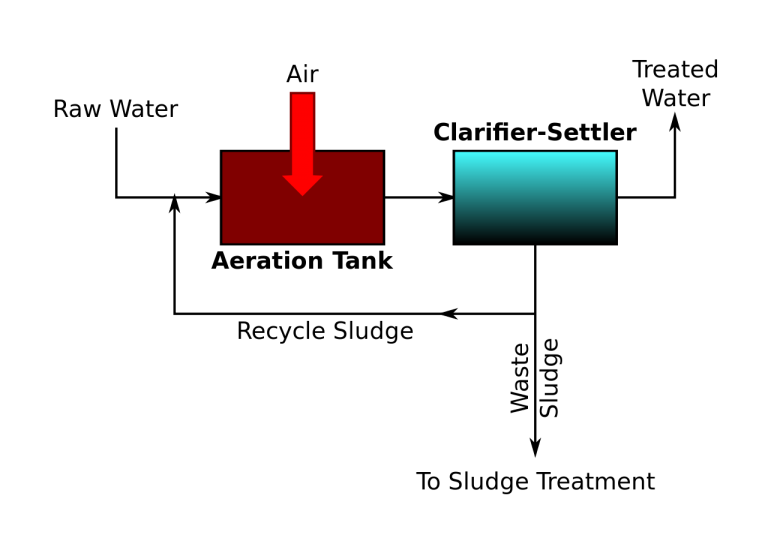
Biological treatment processes are an important component in many wastewater treatment systems. They are one of the most efficient and effective ways of reducing organic material in wastewater. There are quite a few of them that have been researched and used over several decades. However, one of the most widely used conventional biological treatment process is the activated sludge process (ASP). Many sewage treatment plants use ASP in their secondary treatment steps due to the human and animal organic matter in the inlet waters of wastewater treatment plants.
The term “activated sludge” comes from the fact that the sludge contains live bacteria and protozoa that actively digest and break down sewage. It is different from the sludge solids removed following a settling process in that way, with the addition of being odorless.
The process itself involves pumping the effluent from the primary treatment clarification step into a large tank that contains the activated sludge. The mixture is subjected to aeration, either from submerged or surface aerators. This provides oxygen to the effluent that the bacteria can then use to break down the organic waste material. After a sufficient amount of hydraulic retention time, the resulting slurry is pumped into a clarification system or tank to settle out the remaining solids. The treated water is pumped off from the top to any subsequent polishing filtration and disinfection while the sludge at the bottom is recirculated back to the ASP tank to reseed the leftover activated sludge.
ASP has been proven to obtain decent results in the final quality of the treated water, but it is not without its faults and disadvantages. There are several things to consider before choosing an activated sludge process (ASP) for a municipal, commercial or industrial wastewater treatment application.
We have included 7 potential disadvantages of the conventional activated sludge process to be discussed below.
Hydraulic Retention Time
Perhaps the most important aspect of any wastewater treatment process is time. Any treatment solution needs time to run its course and certain treatments take longer than others. ASP is one of those solutions. Due to the ratio of sewage to sludge and how the process occurs, the hydraulic retention time of ASP can take most of a day (12-24 hrs.) or up to several days (3-5) to achieve appropriate levels of treatment results.
Sludge Retention Time / Recycling
Time also applies to the medium of the reaction. In this case, the medium is the activated sludge. With regards to the sludge itself, an ASP is an open system and there is a different mass rate entering the system than there is exiting the system.
Over time (without a recirculation system) all of the activated sludge in the tank would get pumped out. The idea is to maximize the time the sludge spends in the system. This time is to ensure there is enough biomass to break down the incoming organic matter; hence the need for recirculation.
Therefore, as most suspended growth biological processes or fixed film processes including MBBR have higher sludge retention times, ASP tends to have lower sludge retention times.
Size
Due to both of the points stated above, reactor tanks for the activated sludge process (ASP) tend to be quite large in order to treat larger volumes of effluent. This requires large areas of land needed for their operation.
Changes in Volume or Character of Sewage
ASP can treat large quantities of various organic materials, but the reaction is dependent on variables that make it quite susceptible to error in conditions outside of those it was designed for.
In particular, changes in sewage volume and sewage characteristics can result in decreased treatment quality or treatment upsets. If a treatment plant decided it wanted to increase its treatment volume or began treating wastewater from a new and different source, the ASP reactors would typically need to be completely redesigned accordingly.
Sludge Disposal
As can be expected from dealing with a treatment process that uses sludge to treat sewage, there are considerable volumes of sludge that need to be disposed of after this process. Larger sludge volumes mean higher associated disposal costs.
Operation / Supervision
Biology is a complex subject, therefore, it stands to reason that a biological water treatment process would be complex in certain aspects. On a broad scale, the overall process seems simple enough. However, the design and operation of an Activated sludge reactor typically requires experts in biological systems design to monitor it. A system like this needs a little more skilled supervision than just watching out for mechanical failures and monitoring pH. There needs to be highly skilled operators and supervisors that can check for the viability and efficiency of the bacteria and protozoa in the sludge to prevent system upsets.
Issues with Sludge Settling
Some of the biggest issues with the activated sludge process reveal themselves in how everything settles out in the secondary clarification process. Sometimes, the solids don’t compact very well at the bottom and the sludge has high water content.
Sometimes, the supernatant (floating material) has higher turbidity than you want which can affect the end effluent water quality. Other issues can result in decreased concentrations of return activated sludge.
If you aren’t sure that a conventional activated sludge treatment process is right for your municipality or company, and want a more advanced optimized wastewater treatment solution call Genesis Water Technologies, Inc. at 1-877-267-3699 or email us at customersupport@genesiswatertech.com.
We will help you figure out how to optimize and convert your activated sludge process to take advantages of the benefits of advanced GWT moving bed bioreactor (MBBR) technology.