Silica Scaling Prevention in Boilers: Comprehensive Solutions for Industrial Efficiency
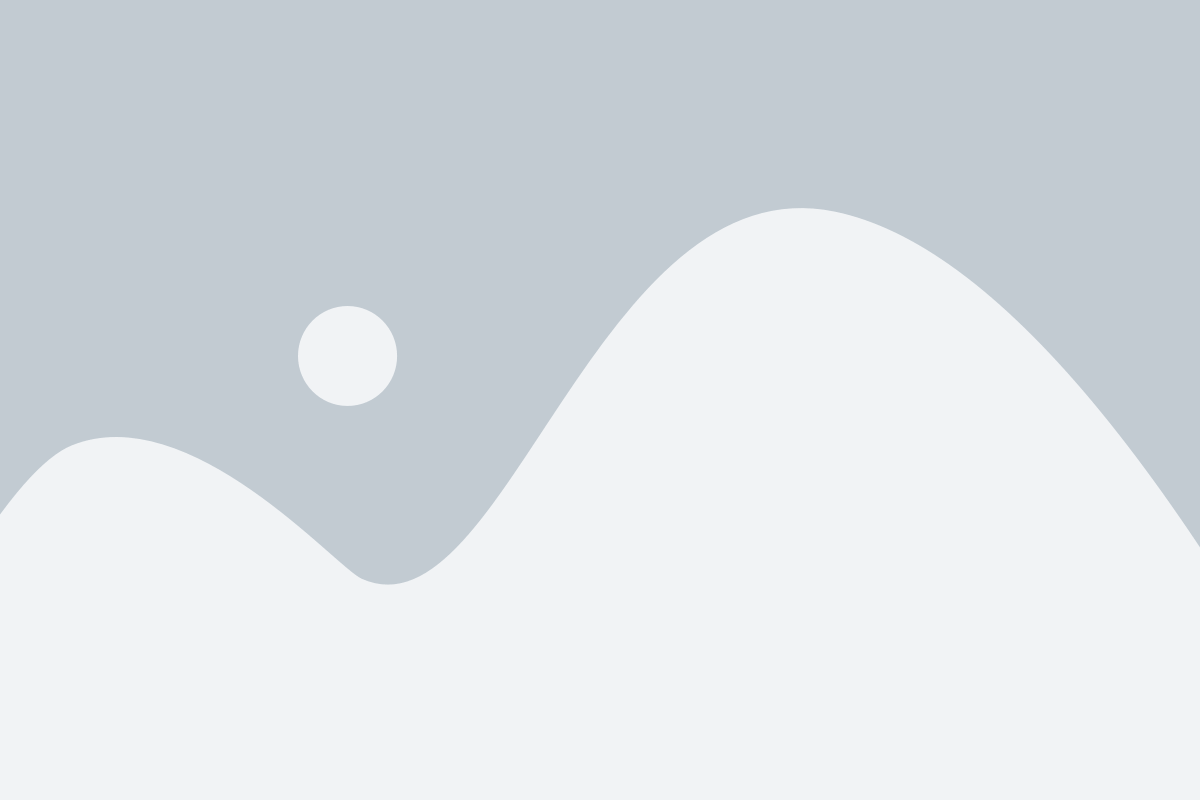
Silica Scaling Prevention in Boilers: Comprehensive Solutions for Industrial Efficiency
Boilers are essential for many industrial processes, but they’re also prone to silica scaling. This buildup impacts boiler efficiency and leads to costly repairs. Effective silica scaling prevention in boilers is critical for maintaining operational efficiency and extending the lifespan of your equipment. This post explores the problems silica scaling causes and offers effective solutions. We’ll examine how Genesis Catalytic Activation Treatment (GCAT) pretreatment, combined with reverse osmosis (RO) and nanofiltration, provides a comprehensive approach to tackling silica scaling.
Table of Contents:
- The Perils of Silica in Boiler Systems
- Common Culprits: Pinpointing Silica Sources
- Traditional Methods: Their Limits and Gaps
- A Better Way: Silica Scaling Prevention in Boilers with Advanced Pretreatment
- GCAT: The Catalyst for Change
- RO and Nanofiltration: The Filtering Duo
- Combining GCAT, RO, and Nanofiltration
- Advantages of this Three-Pronged Approach
- Real-World Example: GCAT and Specialized Membranes in Action
- FAQs about Silica Scaling Prevention in Boilers
- How to control silica in a boiler?
- How do you prevent silica scaling?
- How to prevent scale formation in boilers?
- What causes high silica in boiler water?
- Conclusion
The Perils of Silica in Boiler Systems
Silica, often hidden in boiler feed water, can form a rock-hard boiler scale on heat transfer surfaces. This occurs when the solubility limits of silica are exceeded due to increased temperature and pressure inside the steam boiler.
This scale creates an insulating layer, restricting heat transfer. This forces the boiler to work harder, consuming more energy to generate steam. Over time, this leads to overheating, boiler tube failures, unscheduled downtime, and financial losses.
Common Culprits: Pinpointing Silica Sources
Silica enters boiler feedwater from various sources, both natural and industrial. Surface water and groundwater often contain dissolved or reactive silica. Industrial wastewater, especially from processes using water treatment chemicals with high silica content, also contribute.
Even condensate return lines can reintroduce silica. Most water contains dissolved silica, making boiler feedwater susceptible to contamination from multiple points.
Identifying the source is crucial for effective silica scaling prevention in boilers.
Traditional Methods: Their Limits and Gaps
Traditional silica control methods include blowdown and chemical treatment. While helpful, they have limitations.
Blowdown removes water with high silica but does waste plenty of treated water and energy. Conventional chemical treatments can prevent scale formation but require careful monitoring and adjustments. Traditional approaches might increase operating expenses without fully resolving the issue.
A Better Way: Silica Scaling Prevention in Boilers with Advanced Pretreatment
Advanced pretreatment using GCAT, combined with reverse osmosis or nanofiltration membranes, provides a robust solution.
This combination tackles common feed water contaminants in your boiler system, including calcium magnesium hardness scale.
GCAT: The Catalyst for Change
GCAT is a specialized catalytic treatment system that enhances the efficiency of RO systems in feed water. It utilizes both charge neutralization as well as structural modification of the silica molecule to effectively enable the RO membranes to optimally treat both colloidal and reactive silica without with membrane damage. This optimizes RO permeate recovery rates and minimizes the operating cost of the RO unit.
RO or Nanofiltration: The Filtering Duo
Reverse osmosis and nanofiltration have high rejection rates for dissolved minerals like silica. Applied after GCAT, they deliver near silica-free boiler feedwater.
Combining GCAT, RO, or Nanofiltration with small dose antiscalant.
These technologies can work best together. GCAT performs most of the pretreatment, allowing the RO or nanofiltration membranes to focus on fine silica removal.
Advantages of this Three-Pronged Approach
- Reduced silica scaling minimizes scale formation.
- Lower operating costs due to prevented energy loss.
- Extended boiler lifespan from reduced scaling and improved heat transfer.
- Environmentally friendly through less wastewater and chemical treatment. This optimized water treatment solution helps generate steam more efficiently.
- Lower maintenance with less cleaning needed for heat transfer surfaces.
Real-World Example: GCAT and Specialized Membranes in Action
A power plant facing boiler shutdowns due to silica scaling adopted GCAT, RO, and a small dose of specific antiscalant.
Silica levels in their boiler feedwater drastically decreased. Maintenance of the RO system was reduced, and operational permeate recovery and efficiency increased significantly.
Their return on investment extended beyond financial gains, ensuring the plant could operate without constant shutdowns and expensive boiler tube replacements or cleaning.
This example demonstrates how generating steam without interruption leads to a safer, and more reliable industrial water treatment process.
Conclusion
Silica scaling prevention in boilers is vital for smooth operations and cost savings. By understanding silica’s behavior and implementing comprehensive treatment methods, including specialized equipment like GCAT, reverse osmosis or nanofiltration, you can prevent scale and improve boiler performance.
This will contribute to optimizing boiler operation by reducing silica, hardness scale, enhancing RO system recovery rates and lowering your overall industrial boiler operating expenses, and preventing costly repairs.
Take Action Today! Don’t let silica scaling hinder your industrial operations. Invest in advanced water treatment solutions to protect your boilers and ensure uninterrupted, efficient performance.
Ready to learn more? Contact the water treatment specialist at Genesis Water Technologies today at +1 321 280 2742 or via email at customersupport@genesiswatertech.com to sustainably optimize your water treatment process and keep your systems running smoothly.
FAQs about Silica Scaling Prevention in Boilers
How to control silica in a boiler?
A combination of methods works best.
Integrate pretreatment solutions, like GCAT and small dose antiscalant if required before reverse osmosis or nanofiltration systems.
This general boiler approach increases operational efficiency and lowers maintenance needs.
How do you prevent silica scaling?
Pretreat your water supply to lower silica and hardness content. Combining specific antiscalant and a pretreatment method like a GCAT catalytic system for hardness and silica scaling control prior to your RO system to increase boiler performance.
How to prevent scale formation in boilers?
Scale forms when dissolved solids precipitate out of solution. Effective boiler feedwater pretreatment, consistent blowdown, and internal chemical treatment minimize dissolved solids and pH control.
What causes high silica in boiler water?
High silica comes from makeup water, often containing silica from natural or industrial sources. Condensate return can reintroduce silica. Even low silica levels in feedwater increase due to evaporation in the boiler.