Which method is suitable for treatment of heavy metals in paper mill wastewater?
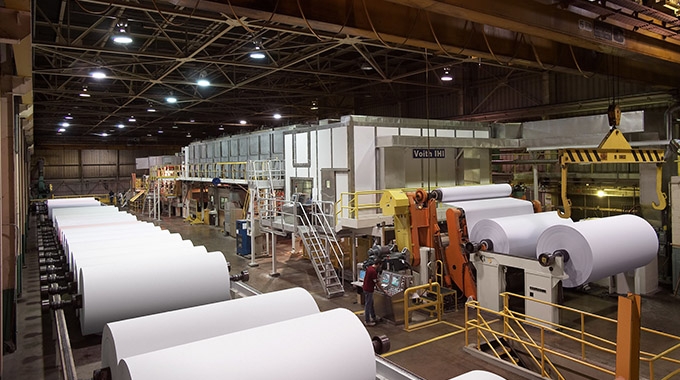
Current issues with paper mill wastewater contaminants
The paper and pulp industry is among the largest industrial users of water resources operating across the world. Typically, pulp and paper industry operations require on average about 54-70 m3 (18,000 gallons) of water per metric ton (2200 pounds) of processed paper goods. This water usage is staggering, and water is used in almost every single part of the pulp and paper manufacturing process. Paper mill wastewater is produced in significant quantities in addition to residual sludge waste from initial pulp digestion to pulp slurry operations and washing the paper making machinery. At least 80% of process wastewater from paper making operations include suspended solids, chemical oxygen demand (COD), trace heavy metals, recalcitrant chlorinated organic compounds, biological oxygen demand (BOD), color and bacteria among others.Therefore, paper companies are looking for advanced treatment strategies and methods for the treatment of heavy metals in paper mill wastewater as well as for the other contaminants mentioned.
Implementation of Advanced water treatment strategies to address these particular issues
In light of these issues, prioritization toward advanced wastewater treatment processes are required to handle these water conditions to optimize this wastewater for environmentally safe discharge or reuse. These viable solutions are specifically provided for paper companies to assist them in harnessing their paper mill wastewater resources in a sustainable way while meeting ever changing regulatory guidelines.
The case for modular wastewater treatment implementation for paper mills operations
Modular wastewater treatment implemented onsite is imperative in many cases due to the volume of wastewater and amount of contaminants in pulp and paper operations. Common treatment technologies include primary treatment for removal of larger suspended solids and particles, followed by coagulation and flocculation using either specialized electrocoagulation and/or specialized flocculants like Zeoturb bio organic liquid flocculant based on the treatment flow rate of the pulp and paper mill. Additionally, biological treatment has been used along with tertiary treatment. This includes advanced oxidation, natzeo media, activated carbon and membrane treatment systems which can allow for higher quality water that can be sustainably discharged or effectively reused in paper mill facility operations.
This treated water can also be used to potentially recharge aquifers, which is particularly important in coastal areas where saltwater intrusion of ground water is an issue.
Strategies to optimize water consumption in paper mill operations
If you are researching strategies to optimize your paper mill facilities water consumption, I have included a few notable points that your facility can apply to enhance daily operations and reduce overall operational costs.
– Plant water treatment process optimization audit
– Consistent care of plant systems
– Integration of advanced modular treatment solutions, including alternatives to the bleaching process.
Reducing water consumption is an ongoing process for pulp & paper facilities, that will require a commitment to sustainability. However, successfully deployed over time throughout these plants, this commitment will provide reduced overall operational costs for the company and enable these facilities to meet ever changing regulations.
Interested to learn more about how specialized electrocoagulation and Zeoturb technologies can assist your organization with sustainable treatment of heavy metals in paper mill wastewater? Contact the water & wastewater treatment experts at Genesis Water Technologies, Inc. at +1 877 267 3699 or reach out to us via email at customersupport@genesiswatertech.com to discuss your specific situation.
Application Case Study (Pulp/Paper Industry)
Challenge
A large pulp and paper company producing various paper products wanted to sustainably treat their washing waste water prior to discharge to meet stricter regulatory compliance. The reduction of the levels of trace metals were of particular importance to allow for sustainable discharge with minimal environmental impact.
Raw Copper levels: 9.2 mg/l
Raw Nickel levels: 350 mg/l
Raw Zinc levels: 24 mg/l
TDS: 8700-12200 mg/l
pH: 9
Solution
Genesis Water Technologies provided process consulting/design as well as the treatability testing to planned full scale implementation. The system included specialized electrochemical treatment, post clarification, followed by post polishing filtration using Natzeo and carbon media. This shall be accomplished via a continuous batch process.
Results
The treatability results validated by a US accredited third party lab, in which the full scale system will be implemented are included below.
The optimal removal percentage efficiency results are listed below:
Treated Copper levels: >99% reduction
Treated Nickel levels: >99% reduction
Treated Zinc levels: >99% reduction
Capital cost and operation cost shall be optimized based on adjustment of conductivity of the raw source water and post treatment.
If required by changing guidelines, further polishing including TDS reduction can be accomplished via a tertiary RO membrane system.
The sludge production was minimized with a higher solids content that was easy to dewater, therefore, reducing associated disposal costs for the larger wastewater flow rates of this large pulp and paper mill operation.
The implementation of this system will provide treated water within the water quality parameters set by the clients regulatory guidelines to allow sustainable discharge of their wash water in the production of their paper products. This will assist them to reduce the environmental impact of their paper mill effluent operations on the surrounding environment.