Refinery Wastewater: Benefits of Remediation by Electrocoagulation
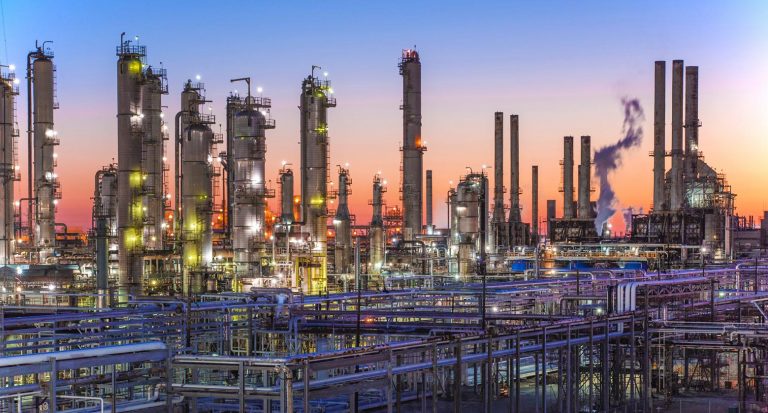
Crude oil is a fossil fuel formed from long-dead organisms subjected to intense heat and pressure underground. This resource is the main ingredient in the production of gasoline, diesel fuel, lubricants, kerosene, propane, and asphalt. All of these products can be made in a single refinery through a complex branching series of chemical processes. The central refining process is atmospheric distillation whereby the crude oil is fractured into different components based on their differing boiling points. Each of these fractions will be sent along to separate process to be turned into the different oil products. Therefore, remediation of refinery wastewater from these different processes can be quite complex.
Complicated, high-temperature processes like these require large volumes of water. It has been estimated that for every barrel of crude oil processed, 1.5 barrels of raw water are used and 70-90% of that water ends up as wastewater. A majority of the water is used in cooling towers, initial desalting process, and also converted to steam for many of the remaining refinery production processes.
Due to all of the chemical processes used in refinement, the wastewater contains pollutants such as:
- Free oil
- Emulsified oil
- TSS
- BOD
- COD
- Sulfides
- Phenols
- Cyanides
- Ammonia
- Hydrocarbons
Ammonia is not toxic to mammals such as humans but is extremely harmful to aquatic species like fish.
Hydrocarbons, phenols, and cyanides are highly toxic to humans and animals. Oils in surface waters can cause issues for aquatic animals and plants.
General regulations for refinery discharge dictate that concentrations of most of these contaminants are to be less than 10 mg/L aside from TSS and BOD which should be less than 20 mg/L and COD less than 200 mg/L.
Many refineries already have water treatment systems for wastewater remediation. They make use of processes like API separation, equalization, aeration, dissolved air flotation, biological processes, chlorination, ultrafiltration, and reverse osmosis. These complete processes can be complex and extensive because so many different treatment methods need to be used in order to make the wastewater acceptable for reuse or discharge.
However, it is possible for oil & petrochemical refinery wastewater remediation to be simplified with the integration of electrocoagulation (EC). EC is a process that has the ability to remove a variety of solids, chemicals, heavy metals, FOG, and pathogens through electrolysis. This process involves oxidation and reduction at the anode and cathode respectively through electrochemistry. Each of these reactions causes the coagulation of heavier solid particles and lighter particles which create floc, that is subsequently separated in a post clarification process.
An EC unit could be implemented downstream of oil separation and solids filtering units that would significantly reduce the concentrations of free oils and hydrocarbons as well as suspended solids before the EC process. Therefore, allowing the EC process to be optimized to reduce emulsified oils along with phenols, sulfides, COD, and BOD. A study of the effectiveness of just these two treatment processes alone can be seen here. Table 1 in this link shows the wastewater concentrations upstream of an API separator while Table 2 offers a comparison of concentrations downstream of the API and certain post-EC concentrations.
With pollution levels already reduced after just two processes, it does not take much more treatment to reduce the levels down to the level required for safe reuse or discharge. This treatment process simplification is one of the major benefits of using EC as part of a solution to remediate refinery wastewater.
A shorter process chain also means faster treatment times and lower capital and operating costs. Shorter process chains also require less space for operation. EC, in particular, is a space-saving and cost-effective treatment solution. The energy consumption for EC is also quite low as the process can achieve good removal rates at an optimized current density and in a short period of time (i.e. 30-60 minutes). Sludge is a common issue with chemical treatment methods, but EC does not typically require chemical additives so sludge production is kept to a minimum, saving on disposal costs.
Electrocoagulation is a burgeoning treatment technology that has great potential in the remediation of refinery wastewater treatment. It’s an effective and efficient treatment that can save a facility money on capital and operating costs and requires less land space for use.
Genesis Water Technologies has specific expertise and experience in specialized electrochemical process train integrations in petrochemical refinery applications.
Do you want to improve the efficiency and reduce the operating cost of your refineries wastewater treatment process system? Call Genesis Water Technologies, Inc. at 1-877-267-3699 in the US or email us at customersupport@genesiswatertech.com for a free initial consultation. We’ll help you discover how to optimize the industrial wastewater treatment process in your refinery operations.