Streamline Seawater Desalination Plant
Maintenance Schedules
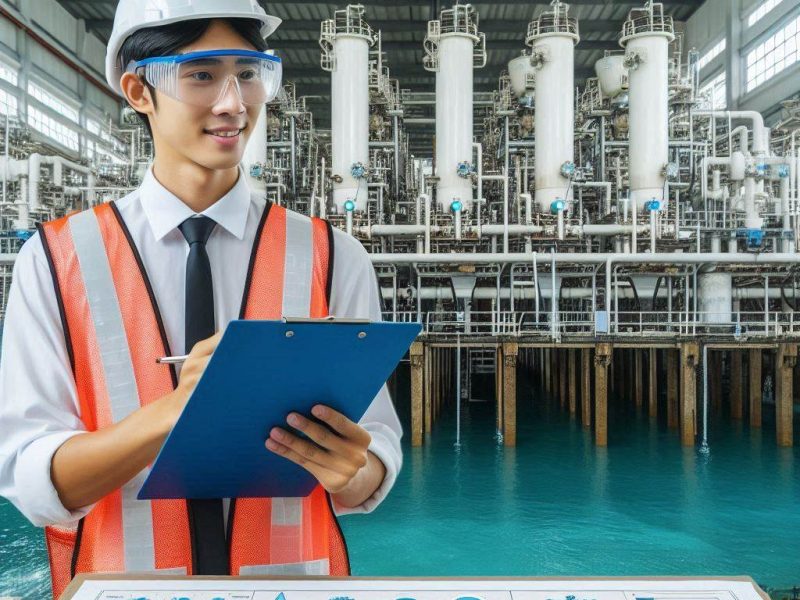
When managing seawater desalination systems, well-defined seawater desalination plant maintenance schedules are critical. But creating a truly effective one requires an understanding that goes beyond routine checkups and maintenance steps. This means considering the unique challenges posed by the marine environment, the complexities of the
desalination process itself, and the specific needs of your plant’s equipment. Neglecting this crucial aspect can result in decreased efficiency, costly downtime, and a shorter lifespan for your valuable assets.
An often-overlooked aspect of robust seawater desalination plant maintenance schedules is the importance of a well-trained staff. We, at Genesis Water Technologies could not emphasize this enough. Just as a car needs a skilled mechanic, desalination plants requires a knowledgeable team to keep them running smoothly. This isn’t just about knowing how to turn a wrench; it’s about understanding the intricate processes involved in reverse osmosis desalination and knowing how to troubleshoot problems before they escalate. Investing in ongoing training for your staff can translate to significant long-term savings and operational efficiency.
Table of Contents:
- Designing a Comprehensive Seawater Desalination Plant Maintenance Schedule
- The Hidden Dangers of Neglecting Maintenance
- FAQs About Seawater Desalination Plant Maintenance Schedule
- Conclusion
Designing Comprehensive Seawater Desalination Plant Maintenance Schedules
This involves understanding two main categories: routine maintenance tasks that need to be performed regularly, and specialized procedures. Let’s break these down in detail:
Routine Maintenance
Think of these tasks as the oil change and tire rotation for your desalination plant, essential for preventing minor issues from turning into major headaches:
Task | Frequency | Focus Area |
---|---|---|
Visual inspection of equipment for signs of wear, leaks, etc. | Daily | Pumps, valves, pipelines, membranes, energy recovery systems, chemical dosing units, etc. |
Monitor and record operational parameters like flow rates, pressures, salinity, chemical dosing, and energy consumption. | Daily/Shift-based | Provides baseline data to detect anomalies quickly, anticipate maintenance needs, and optimize system performance. |
Backwash intake screens. | Daily or Multiple Times a Day Depending on Conditions | Prevents clogging of intake pipes by marine life, debris, and sediment which reduces flow rates and puts a strain on pumps. |
Check and calibrate online instrumentation (pressure gauges, flow meters, salinity sensors, chemical concentration monitors). | Weekly/Monthly | Ensures readings remain accurate to inform operational adjustments, chemical dosing, and detect membrane performance degradation. |
Clean and inspect pre-treatment systems. | Weekly/Monthly | The efficiency of pretreatment directly impacts the longevity of membranes. Regular upkeep (replacement filters, filter media and chemical dosing systems) of these systems are critical. |
Clean membrane surfaces using standard or enhanced flushing procedures. | Bi-weekly to Monthly (depending on feed water quality and operational parameters) | Removes light scaling or biofouling on membranes, maintaining performance. Regular permeate flushing schedules need to be balanced to maximize effect and minimize the impact on membrane lifespan. |
Inspect and test backup generators and emergency shutdown systems. | Monthly | Essential for ensuring continuous operation in case of power failure or unforeseen circumstances. |
Specialized Maintenance Procedures
These involve a deeper level of intervention and are typically scheduled based on operational hours or the specific conditions of your plant:
Task | Frequency | Focus Area |
---|---|---|
Chemical cleaning of membranes using specialized cleaning solutions only as required (targeting specific types of fouling – organic, inorganic, or biological) | Every 3-6 Months (depending on feed water quality, plant operation, and membrane performance indicators such as differential pressure). | Removes stubborn scaling, biofouling, or organic deposits to restore membrane permeability and maintain overall system performance. |
Inspect and service high-pressure pumps (checking for wear of seals, bearings, impeller condition, lubrication). | Every 6-12 Months or based on manufacturer’s recommendations and operational hours. | Maintains pump efficiency and prevents unexpected breakdowns, which could disrupt plant operations and water production. |
Replace pre-treatment filter media (Natzeo, activated carbon). | As needed basis (depending on feed water quality, types of filters, and operational load). | Maintains the efficiency of the pre-treatment system in removing sediments, organic compounds, chlorine, and other contaminants that might damage the desalination membranes. |
Inspect and maintain the integrity of pipelines and valves. | Annually | Checking for corrosion, leaks, blockages to prevent costly downtime, water loss, and environmental contamination due to potential leaks. |
Inspect and service energy recovery systems. | Annually | Ensures efficient energy use by recovering and reusing pressure energy from the desalination process , contributing to cost savings and environmental sustainability. |
Membrane replacement | Every 3-7 Years (depending on operating conditions, pre-treatment efficacy, and cleaning practices). | Maintaining desalination plant performance by proactively replacing aging membranes that experience irreversible fouling or decline in performance even after cleaning, impacting water quality and energy consumption. |
Overhaul or replace major components such as pumps, energy recovery systems, and control systems . | As per manufacturer’s guidelines or when nearing the end of their operational life expectancy. | This long-term approach ensures continued optimal plant performance, minimizes the risk of sudden breakdowns, and ensures compliance with industry regulations and best practices for plant safety. |
The Importance of Professional Training
The complexity of desalination plant operations should never be underestimated. Personnel safety is of the utmost importance. The Veolia 2024-2027 Strategic Program, which heavily focuses on resource sustainability, highlights the critical role of trained personnel in achieving those goals. This training isn’t a one-time event. As desalination technology advances and new challenges arise, it’s important to provide ongoing professional development opportunities for your team. Having employees with in-depth knowledge about water desalination plants will be a huge asset.
The Hidden Dangers of Neglecting Maintenance
While the initial investment in detaled seawater desalination plant maintenance schedules might seem significant, the cost of neglecting these crucial steps is considerably higher. This extends beyond the immediate financial implications; let’s examine those areas often overlooked:
1. Reduced Plant Lifespan
Imagine buying a high-performance car but never changing its oil or rotating the tires. It’ll run, for a while, but eventually, it’s going to break down and it won’t be pretty. The same logic applies to a desalination plant. By neglecting maintenance, you’re essentially accelerating wear and tear on vital components that will be costly if they malfunction.
2. Increased Operational Costs and Energy Consumption
Just like a car engine bogged down with sludge, a poorly maintained desalination plant won’t operate at peak efficiency. A good example of this principle in action is membrane fouling. As EOLSS e-books, a comprehensive resource on desalination and water treatment, explain, membrane fouling increases the energy required to push water through. This means higher electricity bills and less freshwater produced for the same amount of energy. Over time, even small drops in efficiency can add up to massive increases in operating costs.
3. Environmental Risks
Seawater desalination plants, when functioning correctly, contributes to sustainable water management. However, neglect can flip the script. Leaks in the system could result in concentrated brine discharge, potentially harming marine life. Moreover, using more energy to compensate for decreased efficiency has its own environmental consequences, running counter to the principles of sustainable development.
4. Reputational Damage and Public Perception
In a world increasingly focused on sustainability, your plant’s reputation can be impacted if your desalination facility gains a reputation for environmental negligence. Trust is vital when it comes to providing clean water, and failing to maintain your plant responsibly can erode that trust.
FAQs About Seawater Desalination Plant Maintenance Schedules
What is a typical seawater desalination plants maintenance cost?
Providing a specific number for this is challenging without considering various factors such as plant size, complexity, location, and types of desalination equipment used. But what can be said with certainty, neglecting your seawater desalination plant maintenance schedule won’t save you money, it will likely cost you much more down the line due to major repairs, premature equipment replacement, and less efficient operation. Investing in routine maintenance is an investment in the long-term viability and cost-effectiveness of your desalination facility.
Why is proper seawater reverse osmosis desalination plant maintenance important?
A comprehensive maintenance plan minimizes downtime by catching minor issues early on, often before they escalate. Addressing problems promptly keeps your desalination plants up and running, so you can provide a consistent and reliable water supply to those who depend on it. Plus, proper upkeep maximizes the operational life span of equipment and reduces the need for costly emergency repairs or replacements, maximizing the return on investment. It ensures that your valuable resources are being utilized in the most efficient way possible.
Concluding Thoughts
A well-structured seawater desalination plant maintenance schedule is paramount to ensuring the longevity, efficiency, and safety of desalination plants. By investing time, resources, and expertise into creating and executing these maintenance service plans, we not only safeguard our investment but contribute significantly to a more water-secure future. This proactive approach not only minimizes disruptions but also plays a vital role in providing a clean and sustainable water supply for generations to come.
Take a closer look into your seawater desalination plant maintenance schedules?
Contact our team of water treatment experts at Genesis Water Technologies today by phone at +1 321 280 2742 or by email at customersupport@genesiswatertech.com for personalized guidance on maintaining and optimizing your desalination water plants.
Together, we can turn the tide on water scarcity and build a sustainable reliable water supply for future generations to come!